Window and door fabrication are pivotal in modern construction, where energy efficiency, durability, and aesthetic appeal are top production priorities. As building designs evolve, so do the materials and technologies used in window glazing applications. Hot Melt Adhesives (HMAs) have become an essential new technology in manufacturing for this industry, offering more reliable, versatile, and cost-effective solutions for bonding glass to windows and doors. These adhesives are revolutionizing window and door production by significantly enhancing performance, streamlining application with more efficient dispensing methods, reducing labor time, and promoting sustainability through lower emissions and eco-friendly formulations.
A Shift to Cost-Effective, High-Performance Hot Melt Adhesives
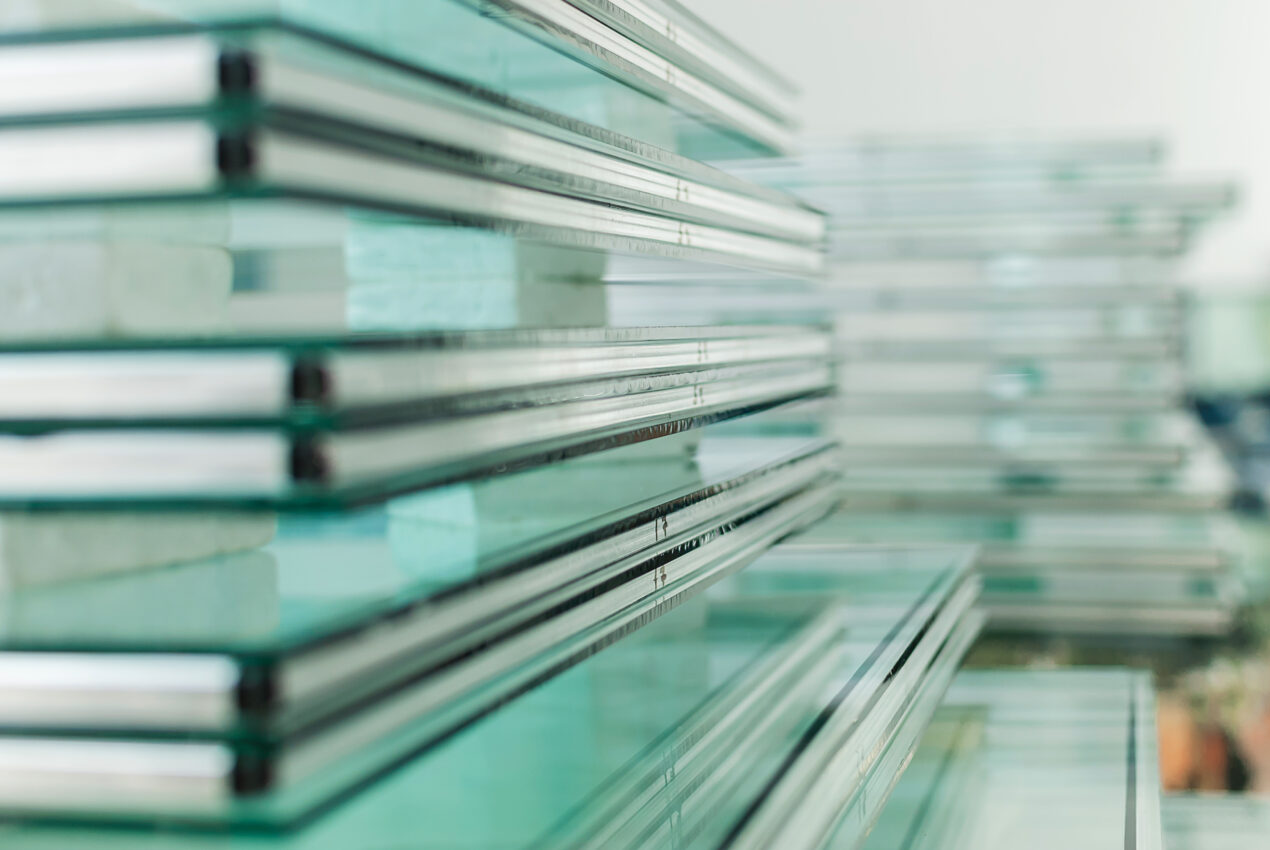
Traditional ‘window glazing’ production has generally relied on double-sided tapes, silicone, and urethane adhesives. However, the shift to HMAs in modern production is driven by superior adhesive performance, simplified dispensing methods, and greater cost-effectiveness. Techniques such as foam sealing in ‘back bedding’ applications offers more efficient process advantages than tapes, silicones and urethanes.
In back bedding for door and window fabrication, foamed hotmelt adhesives are applied using automated dispensers, significantly reducing adhesive costs. These dispensers, integrated with safer linear-bearing systems such as hand-assisted window glazing tables, allow precise application before the glass is set into the adhesive. This method provides an instant, clean bond that eliminates the mess and inefficiency of caulk tubes and other outdated adhesive dispensing techniques.
The transition from silicones and tapes to HMAs brings clear advantages in terms of both cost savings and improved performance, greatly enhancing the efficiency and effectiveness of modern window glazing fabrication.
Hot Melt Innovations in ‘Window Glazing’ Production Methods
- Bonding Glass to Frames: One of the primary applications of HMAs in window glazing is sealing glass panes to frames. Whether in aluminum, wood, or composite frames, HMAs provide a clean, strong, and flexible seal that holds up under various environmental conditions. Their flexibility is essential for absorbing stresses caused by temperature fluctuations and building movement, reducing the risk of glass breakage or frame warping.
- Sash Insulation: Sealing multiple glass units, such as double- or triple-pane windows, is crucial for energy-efficient buildings. HMAs create an airtight bond that prevents moisture infiltration and maintains insulation properties, enhancing the longevity and performance of windows, an essential feature for energy-conscious construction.
- Profile Wrapping: HMAs are also used for attaching decorative elements such as films and surface treatments to windows. These adhesives allow for easy application and removal without damaging glass or leaving residue. HMAs also aid in installing functional components like glazing bars and weatherstrips, enhancing the performance and aesthetics of windows.
- Noise Reduction & Vibration Damping: In urban settings, minimizing noise is essential. HMAs are employed to bond acoustic materials, such as films and panels, to surfaces like windows and walls, aiding in sound dampening and vibration reduction. This application is especially beneficial in high-rise buildings where external noise can be disruptive. For instance, companies like Cattie Adhesives manufacture hot melt adhesives designed for laminating acoustic panels, effectively reducing sound transmission in various environments.
- Safety and Security Applications: Hot melt adhesives (HMAs) are commonly used in the production of laminated glass, which is designed to enhance safety and security by preventing shattering upon impact. In laminated glass, interlayer materials such as polyvinyl butyral (PVB) or ethylene-vinyl acetate (EVA) are bonded between glass layers using heat and pressure, creating a resilient barrier that holds the glass together when broken. This construction is particularly beneficial in high-risk environments like schools, hospitals, and urban high-rises, where maintaining the integrity of glass under stress is crucial.
- Smart Window Technologies: Smart windows, capable of adjusting transparency, tint, and thermal properties, are becoming increasingly popular in modern construction. HMAs are significant to manufacturing these systems, particularly in bonding window layers that enable smart tinting functions. The ability to adhere without interfering with electronic components or optical properties makes these adhesives indispensable for smart window production.
Advantages of Hot Melt Adhesives in Window & Door Manufacturing
The use of HMA’s in the window glazing industry offers several key advantages:
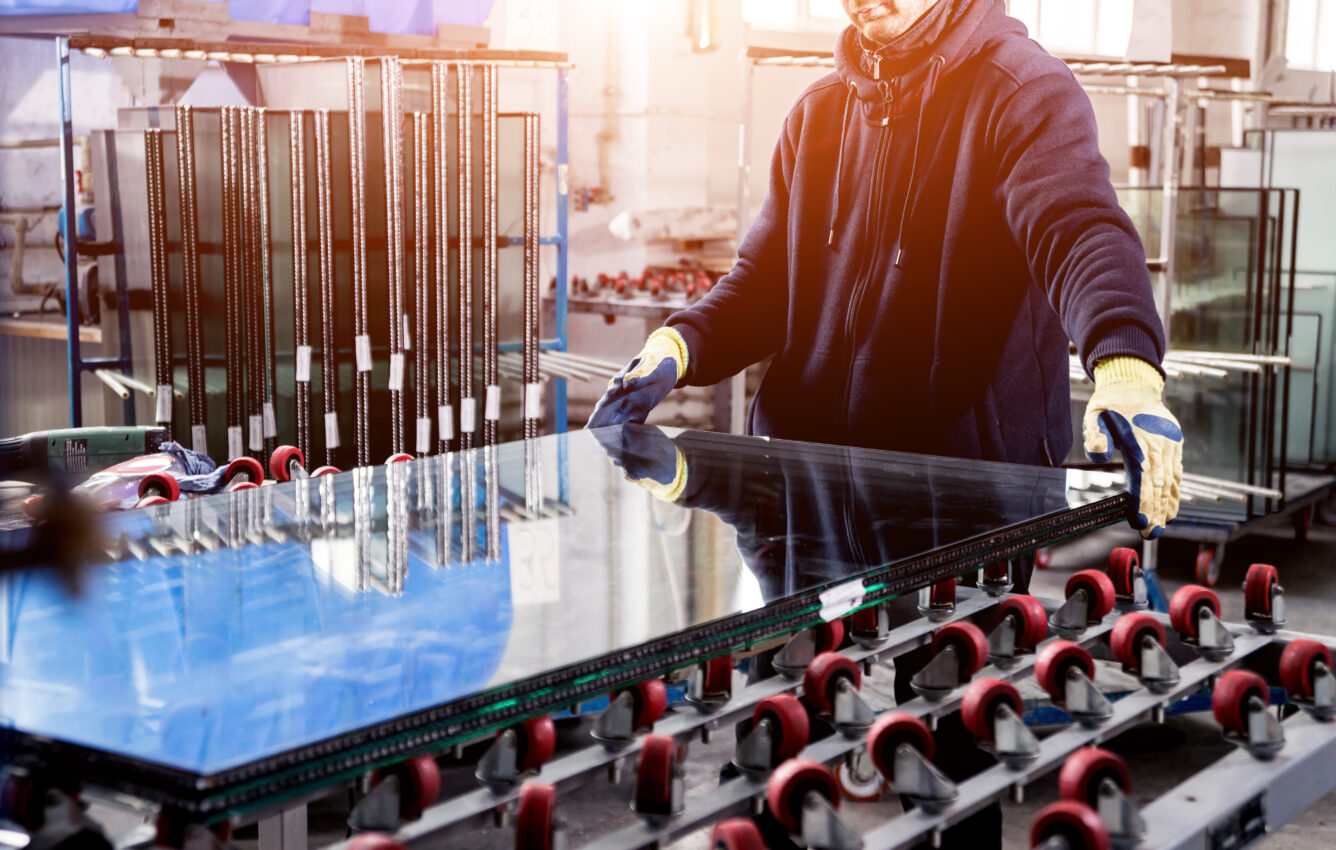
- Efficiency and Ease of Application: HMAs provide an immediate bond upon application, eliminating the need for curing time or specialized equipment. This simplifies the installation process, reduces labor costs, and speeds up project timelines.
- Versatility: HMAs bond a wide range of materials used in window glazing, including glass, metals, and plastics. Their versatility makes them suitable for various applications, from residential windows to large-scale commercial projects.
- Durability & Flexibility: HMAs are formulated to withstand environmental stresses, such as temperature fluctuations, UV exposure, and moisture. Their flexibility ensures that these adhesive bonds remain strong as materials expand and contract, contributing to the long-term durability of windows.
- Aesthetics: HMAs provide a clean, seamless bond that enhance the appearance of windows in modern architectural designs. Their use allows for sleek, unobtrusive joints, complementing minimalistic design trends.
- Sustainability: HMAs provide a low-VOC alternative to traditional adhesives, contributing to healthier indoor air quality in production facilities while also reducing environmental impact. Ongoing advancements in eco-friendly HMA formulations further align with the industry’s increasing focus on sustainability.
Conclusion
Hot Melt Adhesive (HMAs) technologies have revolutionized the window and door manufacturing industries, particularly in glazing, by offering versatile and efficient solutions for bonding, sealing, and enhancing the performance of modern windows. The shift from traditional methods like double-sided tapes and silicones to HMAs, specifically hotmelt adhesives, represents a major advancement in cost-effectiveness, sustainability, and performance standards.
As the window and door manufacturing industry continues to innovate, this new adhesive technology will play an increasingly critical role in addressing the demands of modern construction, where durability, energy efficiency, and aesthetics are paramount, keeping pace with ongoing technological advancements and R&D developments.